ELECTRICAL INFRARED INSPECTIONS
Ensuring Safety and Efficiency
The Power Of Infrared
Thermal imaging is the fastest way to detect hot, defective components in electrical systems. Infrared electrical system scanning is a non-invasive and non-disruptive method of assessing an electrical system’s safety. Certified thermographers scan electrical components to identify hot spots and problem areas — before bad electrical components put your equipment, building, and occupants at risk. Through electrical infrared testing, you will be able to Detect system overloads, loose defective components and damaged switchgear. Infrared electrical testing finds hot, dangerous problems quickly.
At Global Infrared, our infrared electrical inspections provide solutions to emerging and existing issues in electrical and mechanical equipment. We reduce unscheduled downtime due to equipment failures and significantly reduce the risk of electrical fire.
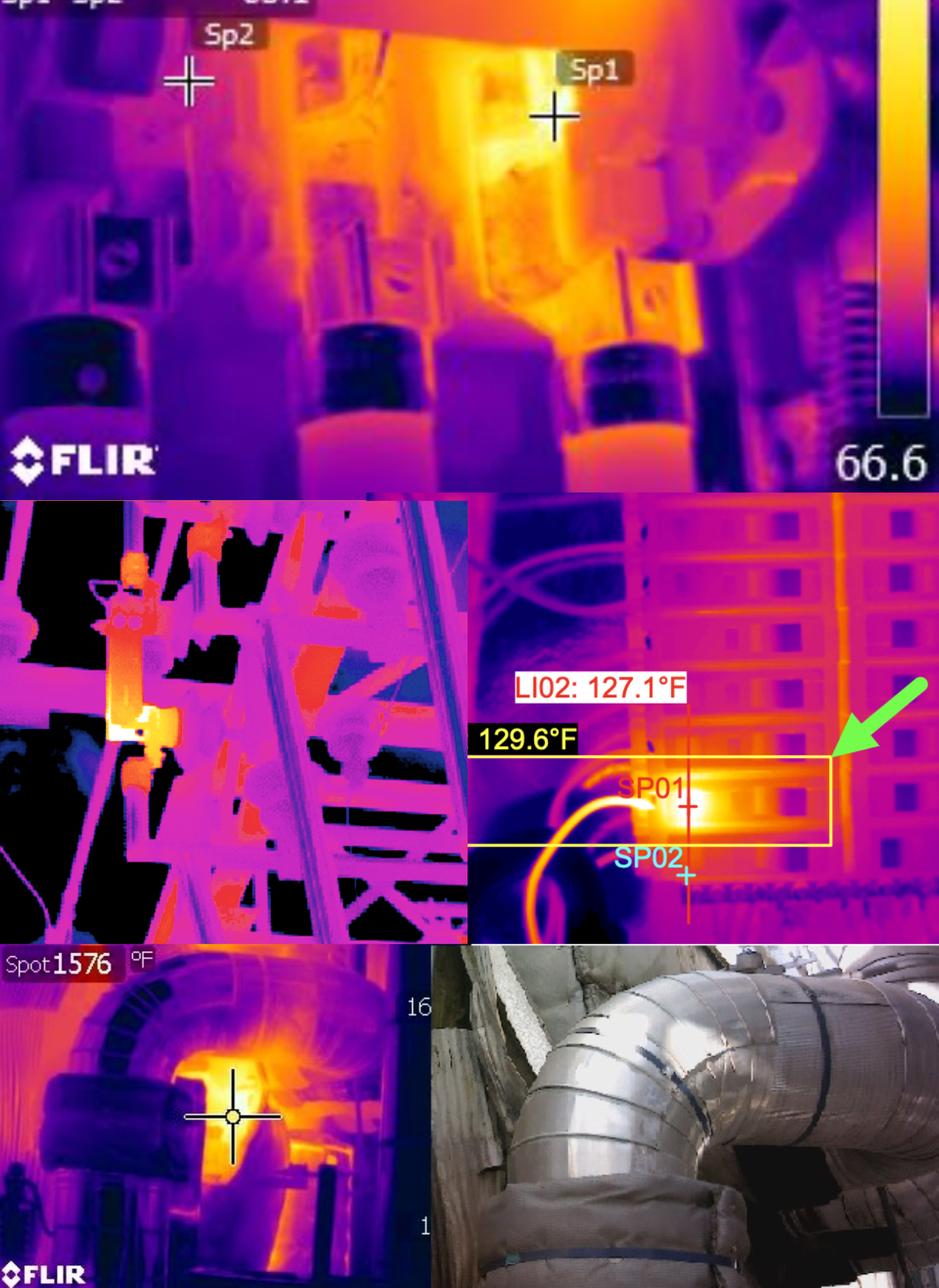
BENEFITS OF INFRARED INSPECTION:
-
Reduce Unscheduled Down Time
-
Increase Equipment Life
-
No Service Interruption During Inspection
-
Protects Employees, Contractors & Civilians
-
Lower Repair Costs
-
Increase Profits
-
Reduce Liability & the Likelihood of an Electrical Fire
-
Lower Insurance Premiums Due to Reduced Losses
-
40+ Years of Confirming Insurance Industry Supporting Data
-
Establish Baseline Thermal Signatures for New Equipment
CONDITIONS DETECTABLE BY AN INFRARED INSPECTION:
-
Loose/Deteriorated Connections
-
Overloaded Circuits
-
Compromised Circuits
-
Unbalanced Loads
-
Inductive Heating
-
Open Circuits
-
Defective Equipment
Thermal Imaging is a service which is non-intrusive and should have no impact on normal business operations.
In order to provide the most accurate and thorough infrared inspection, we must first inspect all areas and devices which are normally running under constant load like elevators, general lighting and laundry rooms etc., we find it is more efficient to chase than to create.
Then we move to the areas which have not been under load, for example: chillers (lead vs. lag) or time of day. This should be documented and noted so engineering personnel can schedule the equipment switch over (at the proper time) for a truly complete inspection of the area. If the equipment is shutdown or is Locked Out & Tagged Out this should also be documented as well, thereby minimizing any possibility of creating a false sense of security. On many occasions we do not work a normal (9 to 5) day throughout the inspection period, this allows us to make ourselves available in the evening or early morning to test Showroom, Night Lighting and or Generating equipment when it is optimal.
The most important factor in any infrared inspection is to ultimately determine the Root Cause of any anomaly found; therefore, we do not incorrectly or prematurely have our client repair or replace any equipment or component without properly documenting the data (amperage, voltage & leakage test) to support such findings. Unlike the computer industry we are not in the component replacement business.
So, bottom line it’s our job to find the more Serious Faults which truly need attention thereby reducing those unnecessary repair costs. If we provide you with this kind of service year after year, then we’ve done our job successfully!




NFPA 70B 2023: New Guidelines for Electric Inspections
In 2023, NFPA70B makes mandatory the inspection of ALL electrical equipment at least every 12 months, with equipment that meets the Equipment Physical Condition 3 requiring thermographic inspection at least every 6 months.